The Importance of 5S
5S is a fundamental pillar of lean manufacturing that emphasizes a clean, organized and efficient workplace. The five steps - Sort, Set in order, Shine, Standardize and Sustain - are essential for maximizing productivity, minimizing waste and ensuring employee safety. When implemented effectively, 5S can lead to significant improvements in quality, delivery time and cost reduction.
Beyond the immediate benefits, 5S fosters a culture of continuous improvement. By creating a visual workplace, employees are empowered to identify and eliminate waste. In addition, 5S fosters a sense of ownership and pride in the work environment, leading to increased job satisfaction and engagement.
The Challenges of Traditional 5S
While the principles of 5S are straightforward, their implementation is often challenging. Traditional 5S methods rely heavily on manual processes such as paper checklists and physical audits. This approach can be time-consuming, error-prone and hinder the ability to track progress and identify areas for improvement.
In addition, maintaining consistency and compliance with 5S standards can be difficult without a centralized system for monitoring and feedback. As a result, the impact of 5S can be limited and the full potential benefits may not be realized.
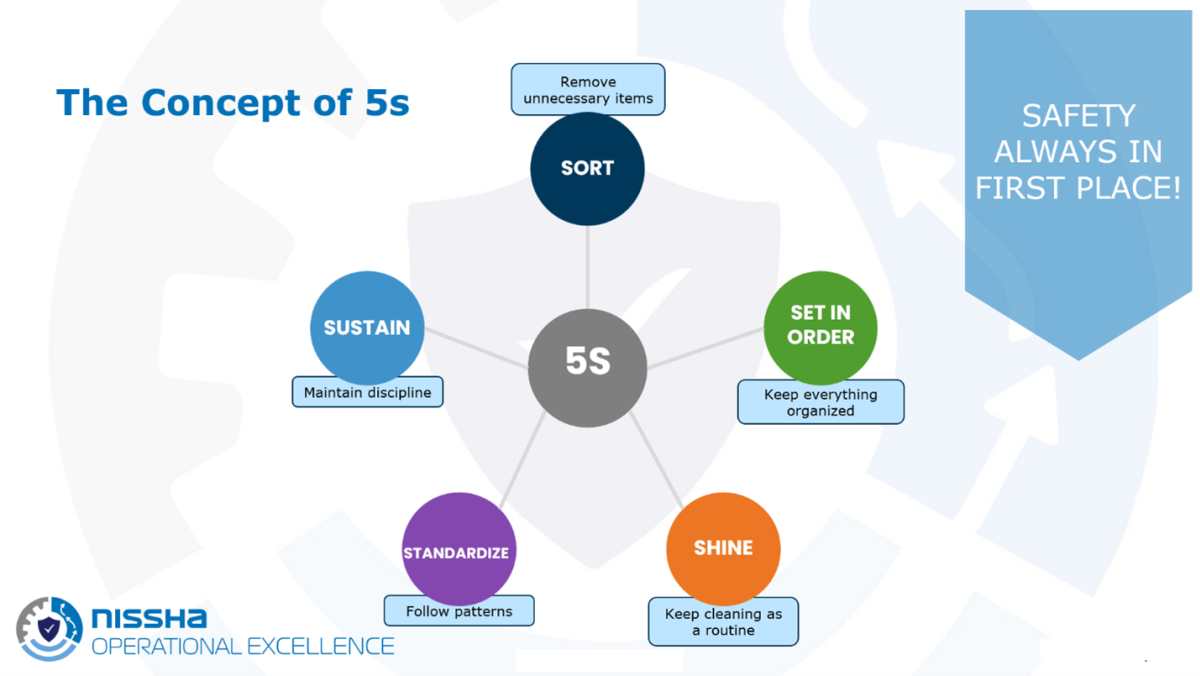
The Digital 5S Revolution
In today’s fast-paced business environment, organizations are seeking innovative solutions to optimize their operations and maintain a competitive edge. The traditional 5S methodology, while effective, can be time-consuming and prone to human error. To address these challenges, organizations are increasingly turning to digital 5S platforms.
Digital 5S platforms offer a comprehensive framework for managing the entire 5S process, from initial audits and implementation to ongoing maintenance and improvement. By leveraging advanced technology, these platforms streamline operations, enhance data accuracy, and provide valuable insights for informed decision-making.
Key benefits of digital 5S include increased efficiency, improved data accuracy, real-time insights, enhanced collaboration, mobile accessibility, and data-driven decision making.
By automating routine tasks, eliminating human error through digital data capture, providing real-time monitoring, facilitating communication and knowledge sharing, enabling mobile audits and inspections, and providing valuable data for decision-making, organizations can revolutionize their approach to workplace organization and efficiency. These platforms empower businesses to create a more organized, productive, and sustainable working environment.
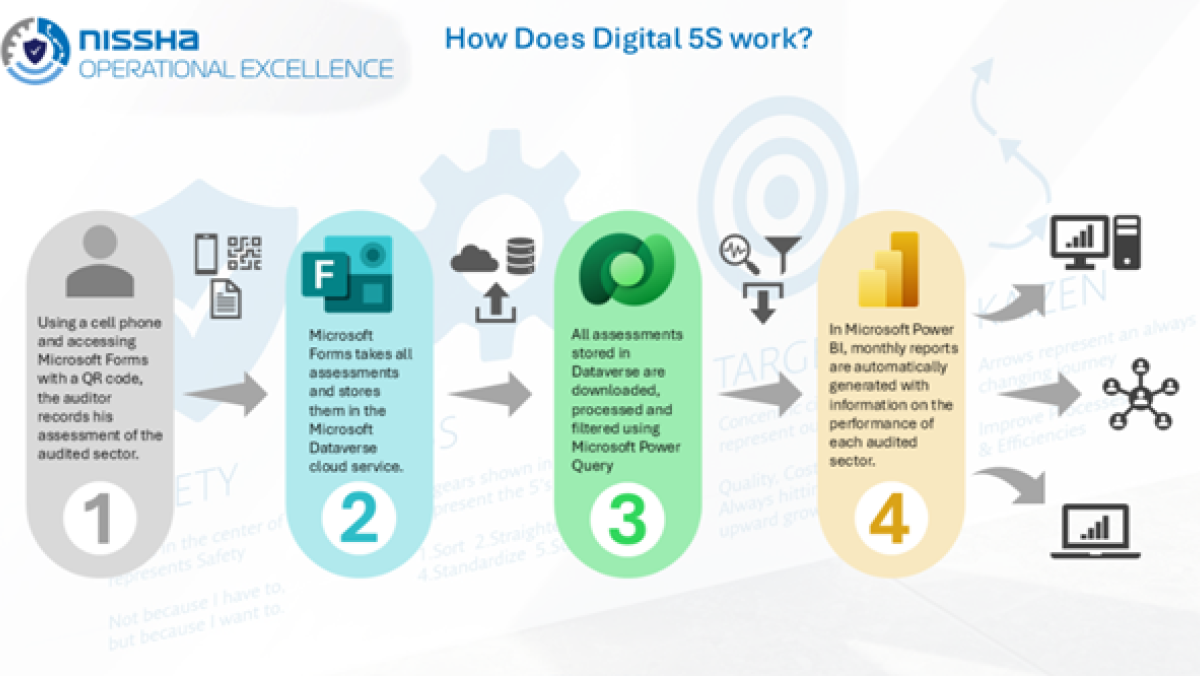
Implementing Digital 5S
Implementing a digital 5S system requires careful planning and execution. To ensure a successful transition, organizations should consider the following steps.
Establish clear expectations and define roles and responsibilities for 5S activities. This will ensure that everyone understands their role in the process and contributes to the overall success of the implementation. Finally, continuously monitor and evaluate 5S performance to identify areas for improvement and make necessary adjustments. This ongoing assessment helps to ensure that the digital 5S system is delivering the desired results.
By following these steps, organizations can successfully transition to a digital 5S system and reap the associated benefits, such as improved efficiency, enhanced data accuracy, and real-time insights.
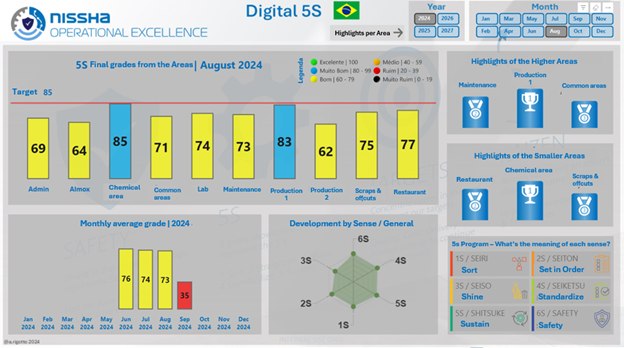
Nissha Metallizing Solutions is committed to operational excellence and continuous improvement. For this purpose, we've fully embraced the Digital 5S revolution. Starting in Brazil, we've integrated Digital 5S into our NMS system, automating many of our 5S tasks for greater accuracy and efficiency. By the end of this year, we expect to have fully implemented Digital 5S at all our sites, including Italy, Germany, Belgium and the United States.
Our NMS system, integrated with Digital 5S, enables us to collect and analyze real-time data using tools such as Customer Voice and Power BI. This data-driven approach allows us to identify trends, measure progress and implement targeted improvements. Regular meetings between process engineers across all sites encourage knowledge sharing and collaboration, driving continuous improvement in our operations.
This technology has empowered our employees to actively participate in maintaining a clean, organized, and safe work environment, resulting in increased productivity and reduced waste. Our commitment to digital 5S demonstrates our dedication to operational excellence and sustainable growth.
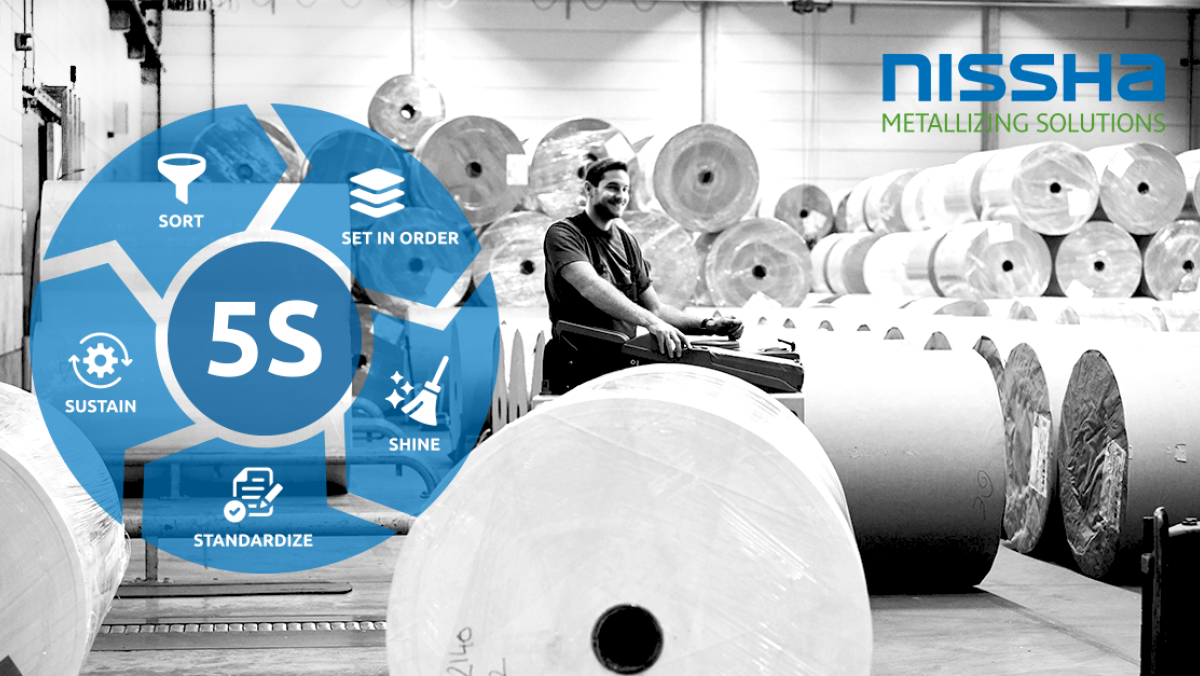
In conclusion, digital 5S represents a significant advancement in lean manufacturing practices. By combining the principles of 5S with the power of technology, organizations can create a more efficient, organized, and sustainable workplace.
Embracing digital 5S is not merely about adopting a new tool; it’s about transforming the way you approach workplace management. By investing in digital 5S, organizations can drive operational excellence, improve employee satisfaction, and achieve long-term success. The benefits of digital 5S are undeniable, making it a strategic investment for businesses seeking to thrive in today’s competitive landscape.