Predictive Maintenance: A Proactive Approach to Asset Management
Unplanned downtime can be a costly and disruptive event for businesses across all industries. Traditional maintenance strategies, such as reactive and preventive maintenance, often fall short in preventing unexpected equipment failures. This is where Predictive Maintenance comes into play.
Predictive Maintenance is a proactive approach to asset management that leverages data analysis and real-time monitoring to predict and prevent equipment failures before they occur. By using advanced technologies like sensors, artificial intelligence, and machine learning, Predictive Maintenance identifies potential issues early on, allowing for timely maintenance interventions and minimizing downtime.
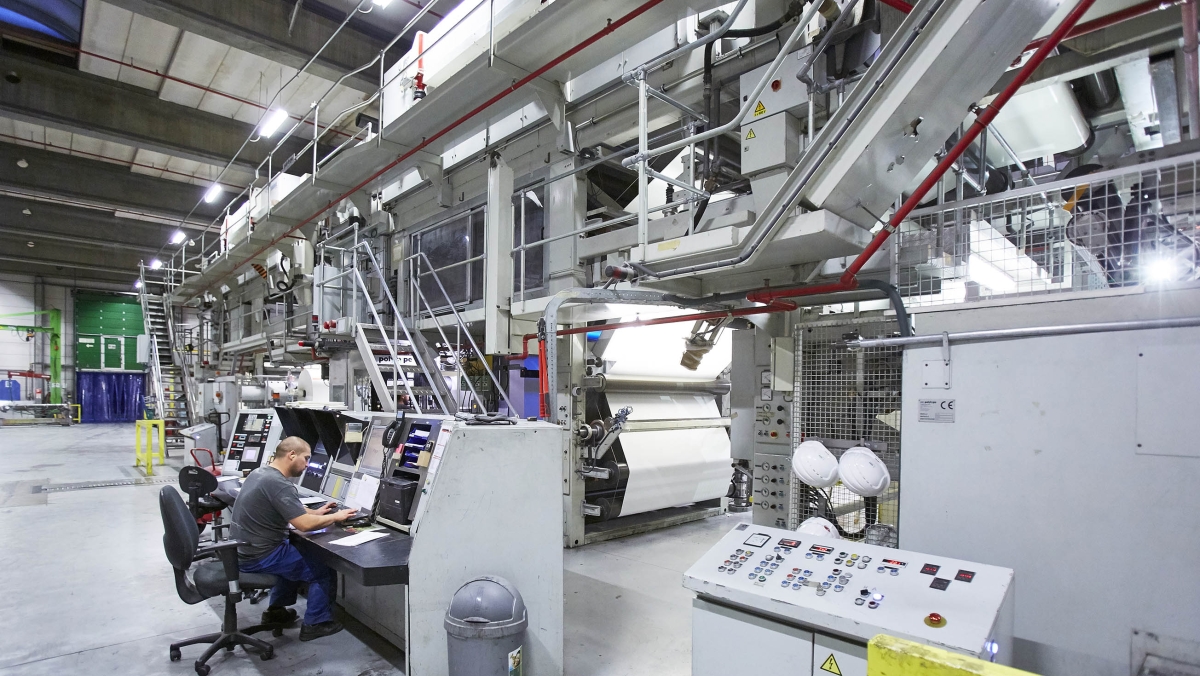
The Limitations of Traditional Maintenance
The limitations of traditional maintenance strategies can have a significant impact on operational efficiency and cost-effectiveness. Reactive maintenance, which involves a “wait-and-see” approach, can lead to substantial losses due to unexpected equipment failures. When a breakdown occurs, it can result in unplanned downtime, lost production, and potentially unsafe working conditions. While preventive maintenance, with its scheduled inspections and replacements, aims to mitigate these risks, it can also have drawbacks. Predetermined intervals may not always align with actual equipment needs, leading to unnecessary maintenance costs and the potential for premature component replacement. This can result in wasted resources and reduced equipment lifespan. To address these challenges, organizations are increasingly turning to predictive maintenance which allows more targeted and efficient maintenance interventions.
The Predictive Maintenance Solution
Predictive maintenance offers a more efficient and effective approach to equipment maintenance compared to traditional methods.
One of the most significant benefits of predictive maintenance is its ability to reduce downtime. By identifying and addressing potential equipment failures before they occur, businesses can prevent unplanned outages, minimize disruptions to production, and avoid the associated costs of lost revenue and productivity. Moreover, predictive maintenance can optimize maintenance costs by ensuring that maintenance activities are performed only when necessary. This eliminates the need for unnecessary repairs and replacements, resulting in significant cost savings.
In addition to reducing downtime and costs, predictive maintenance can also extend the lifespan of equipment. By proactively addressing potential issues, businesses can prevent the deterioration of equipment components, reducing the likelihood of costly replacements. This not only saves money but also improves the overall reliability and efficiency of operations.
Furthermore, predictive maintenance plays a crucial role in enhancing safety. By identifying and addressing potential safety hazards before they lead to accidents or injuries, businesses can create a safer working environment for their employees. This proactive approach to safety can help to protect the well-being of workers and reduce the associated costs of accidents and liability.
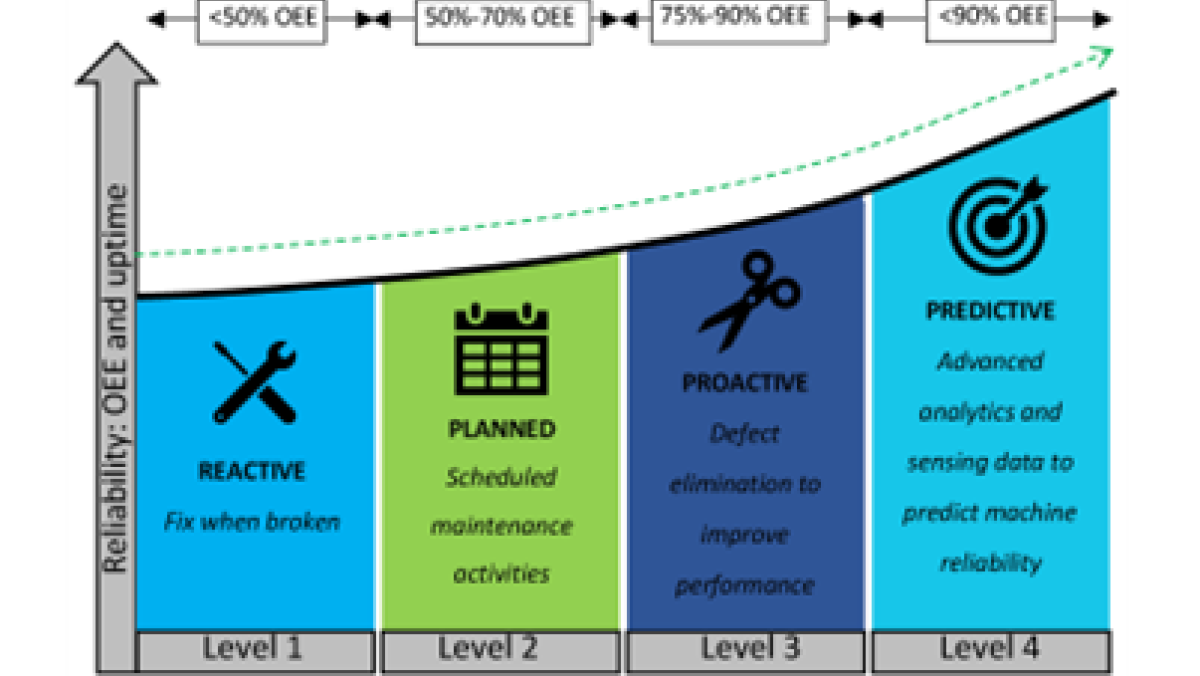
How does Predictive Maintenance work?
At the heart of predictive maintenance lies the integration of advanced technologies, such as sensors, data analytics, and machine learning, to anticipate and prevent equipment failures.
Sensors, strategically placed on critical equipment, serve as the eyes and ears of the system. They collect real-time data on various operational parameters such as vibrations, temperature, pressure, and current, gathering valuable data that provide insights into the equipment’s health and performance. The collected data are then transmitted to a central system for storage and analysis.
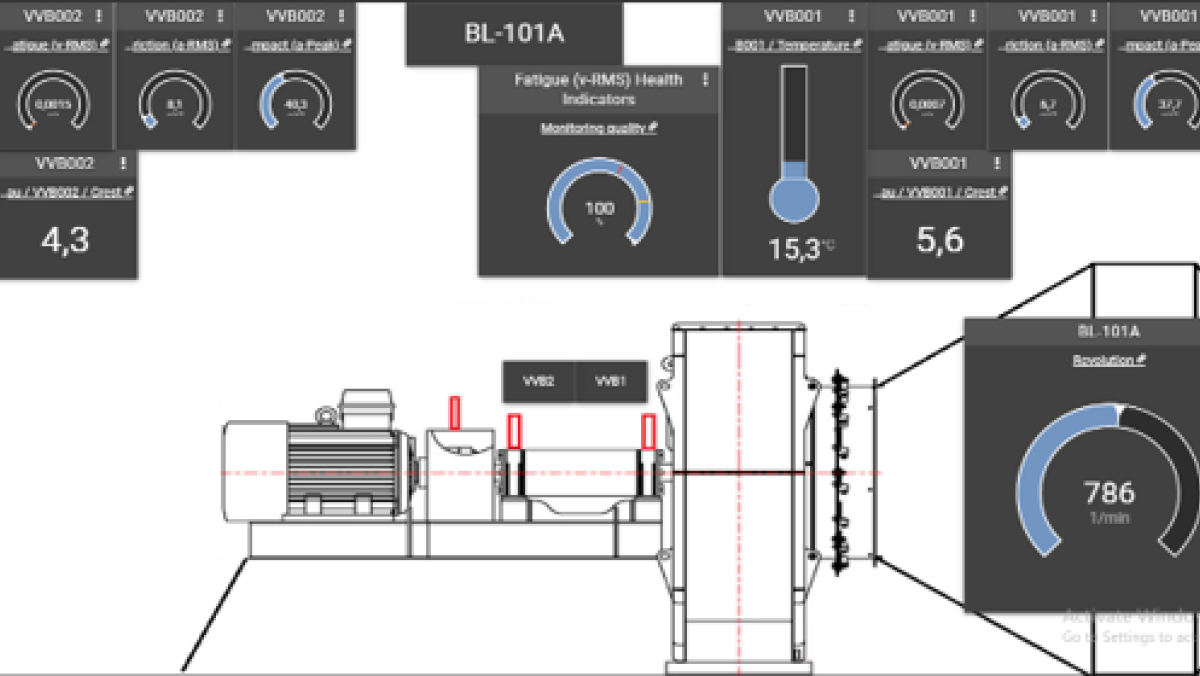
Advanced analytics techniques, such as machine learning and artificial intelligence, are crucial for extracting valuable insights from vast amounts of sensor data. By identifying patterns, trends and anomalies within this data, predictive maintenance systems can accurately anticipate equipment failures. For instance, machine learning algorithms, such as time series analysis and anomaly detection, can analyze historical data to identify recurring patterns and deviations from normal behavior. By learning from past failures, these algorithms can predict future occurrences, allowing maintenance teams to prioritize tasks based on risk. In turn, artificial intelligence techniques, such as deep learning, can analyze complex data sets and uncover hidden patterns that are undetectable to human analysts.
Deep learning models process large volumes of sensor data, detecting subtle changes that signal incipient equipment failure. This enhanced predictive capability enables maintenance teams to make informed decisions and optimize maintenance schedules.
Implementing Predictive Maintenance
This proactive approach can lead to substantial cost savings, improved operational efficiency, and enhanced equipment reliability.
However, successful predictive maintenance implementation requires careful consideration of several key challenges. Ensuring data quality is paramount, as inaccurate or incomplete data can lead to unreliable predictions. Establishing a robust infrastructure to collect, store, and analyze vast amounts of data is essential for deriving actionable insights. Additionally, providing comprehensive training to employees involved in predictive maintenance activities is crucial for maximizing the benefits of this technology.
By investing in high-quality sensors and data collection systems, developing efficient data management and analysis processes, offering targeted training programs, and continuously monitoring and refining their predictive maintenance strategies, businesses can overcome these challenges and reap the rewards of predictive maintenance.
At Nissha Metallizing Solutions, we’re committed to process digitalization and the integration of AI/IoT applications into our operations and logistics. By investing in these technologies, we've successfully implemented predictive maintenance to enhance our operational efficiency and minimize downtime. To date, approximately 50 sensors have been installed at our Italian site collecting real-time data on various equipment parameters. We plan to extend the installation to other sites in the coming months, starting with Germany and followed by Belgium, Brazil and the United States. Specialized software, Moneo, processes this data, leveraging AI algorithms to identify potential issues and trigger alerts when critical thresholds are exceeded. This strategic focus on digitalization and AI/IoT has enabled us to identify and address potential equipment failures before they occur, optimize maintenance schedules, extend the lifespan of our equipment, and improve overall productivity. These benefits have been significant, demonstrating the value of predictive maintenance in enhancing operational performance and reducing costs.
We began our predictive maintenance journey by focusing on the extraction fans of our coaters, which are essential to the operation of our solvent recovery system. These fans are so critical that their failure would require a complete shutdown of the plant. After collecting a month's worth of data, we analyzed it using our predictive maintenance algorithms. The system successfully detected abnormal vibrations in the bearings of one fan, allowing us to schedule preventive maintenance and avoid a costly production stoppage. In another instance, we installed pressure switches to monitor the cooling coils of the solvent-laden air. The sensors detected a drop in pressure in one of the coils, indicating a possible blockage. By proactively addressing this issue, we prevented excessive energy consumption and saved the cost of replacing the coil. These successful implementations highlight the potential benefits of predictive maintenance in improving efficiency and minimizing costs.
Our unwavering commitment to continuous improvement ensures that customers consistently benefit from enhanced products and services. By continually investing in innovation and development, we strive to stay ahead of industry trends and deliver exceptional value. This commitment translates into tangible benefits for customers as our offering continues to evolve to meet and exceed their expectations.
The successful implementation of predictive maintenance can lead to significant cost savings and improved overall productivity. As technology continues to advance, predictive maintenance is poised to become even more sophisticated and effective. Emerging technologies such as the Internet of Things (IoT), artificial intelligence, and machine learning are driving innovation and enabling businesses to achieve even greater benefits. By embracing this proactive approach, businesses can enhance their operational resilience, stay competitive, minimize risks, and achieve long-term success.