Training and knowledge sharing
AR Metallizing is incredibly proud of it’s most unique and exceptional quality: our workforce. So how do we use training and knowledge sharing help us improve performance?
Here at AR Metallizing, we're incredibly proud of our most unique and exceptional quality: our workforce. Having such a skilled, knowledgeable and loyal team helps keep us competitive. We also use training and knowledge sharing as tools to help us continually improve our performance. Here's how:
Training
When we implement new programs and systems, we invest in training for the team to help optimize the use of the new technology. ‘In early November, Stefano Bianciotto and Mauro Bruno joined the Oracle Cloud Day in Milano, as part of our implementation of Oracle FCCS for financial consolidations, for example,’ says Leonie Wolters, Vice President Human Resources. ‘Rather than viewing this as just a way to get to know a system better, we also encourage staff training because it helps our team understand the full functionalities of the system. We want to give our team the training and tools to enable them to come back in-house understanding how they can best leverage a system and identify new areas and ways to use it that we may not yet have identified,’ continues Leonie.
A commitment to sharing knowledge
We encourage knowledge sharing between our global teams: getting our staff together to share ideas and explore how they are overcoming challenges in their respective plants is key. It is our aim that we are always improving product quality and continuing to find ways to make our operations even leaner.
While we’re in agreement that today’s technology and digital tools are great for communication, sometimes, nothing beats face-to-face discussions and explanations, and we often have members of our team travel internationally to work at a different factory to explore practices in another country.
‘The basis for creating metallized paper is more or less the same in all AR Metallizing’s factories, but machinery and manufacturing processes differ slightly from plant to plant,’ says Leonie. ‘This means that there is opportunity to look at how we can improve: what works really well in one plant that could be implemented in another? How can we consolidate successes globally? Each plant has an individual set of strengths, and as a business we work so that knowledge of these strengths can be shared,’ says Leonie.
Being able to ‘bounce’ ideas around with a colleague who truly understands our products, their ways and what our customers and partners require from us, but who has fresh vision because they work at a different AR Metallizing plant is incredibly useful. For example, Tiago Tolentino from Brazil recently spent some weeks in Italy, Diego Donetto from Italy supported Brazil with the set-up of some machinery and Alfredo Durando from Italy spent a longer period in the US to help training operators and new supervisor optimizing data processes flows. ‘It’s an investment to run these exchange programs where a member of the team spends time at another plant, but everyone reaps the rewards. The best part is that we can implement changes and evolve our ‘best practices’ and we pass these on to our customers by producing better products from a leaner supply chain. This is very satisfying both individually and as a team,’ says Leonie.
Powered by a first-class team
AR Metallizing is incredibly proud of it’s most unique and exceptional quality: our workforce. ‘We’re so fortunate to have such a skilled, knowledgeable and loyal team – it’s not unusual for our operators to have been with us for several decades, for example. It is also not unusual for our employees to go the extra mile by coming in extra hours or spend more time in the plant to meet project milestones or to support important customer trials. Everyone is always open and motivated to support in ay way they can to make to company stronger. This makes me very grateful. It is the team’s combined expertise, dedication and intrinsic understanding of our machinery, operations, customer and partner needs and desire to uphold a fantastic quality product that keeps us competitive,’ says Leonie.
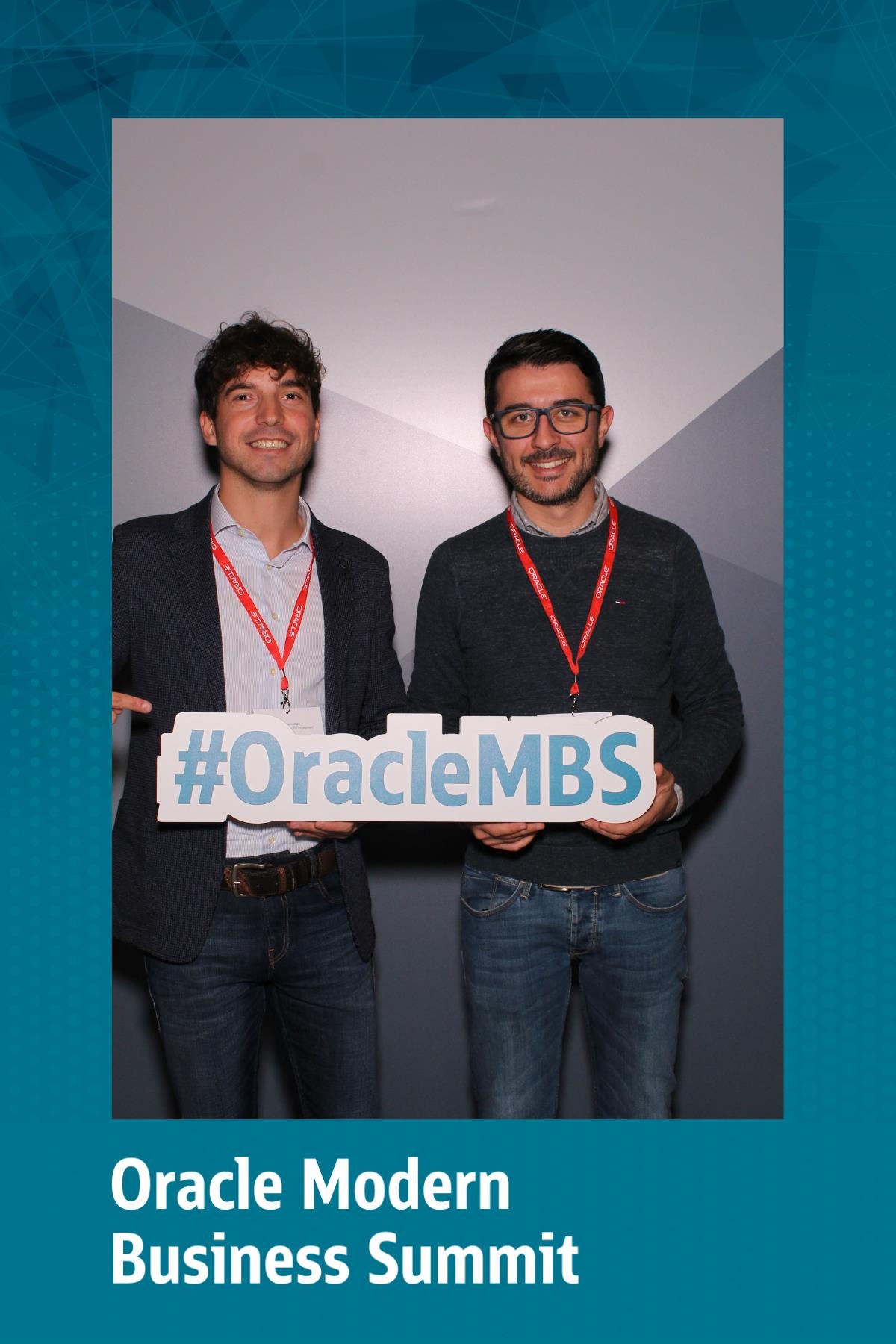